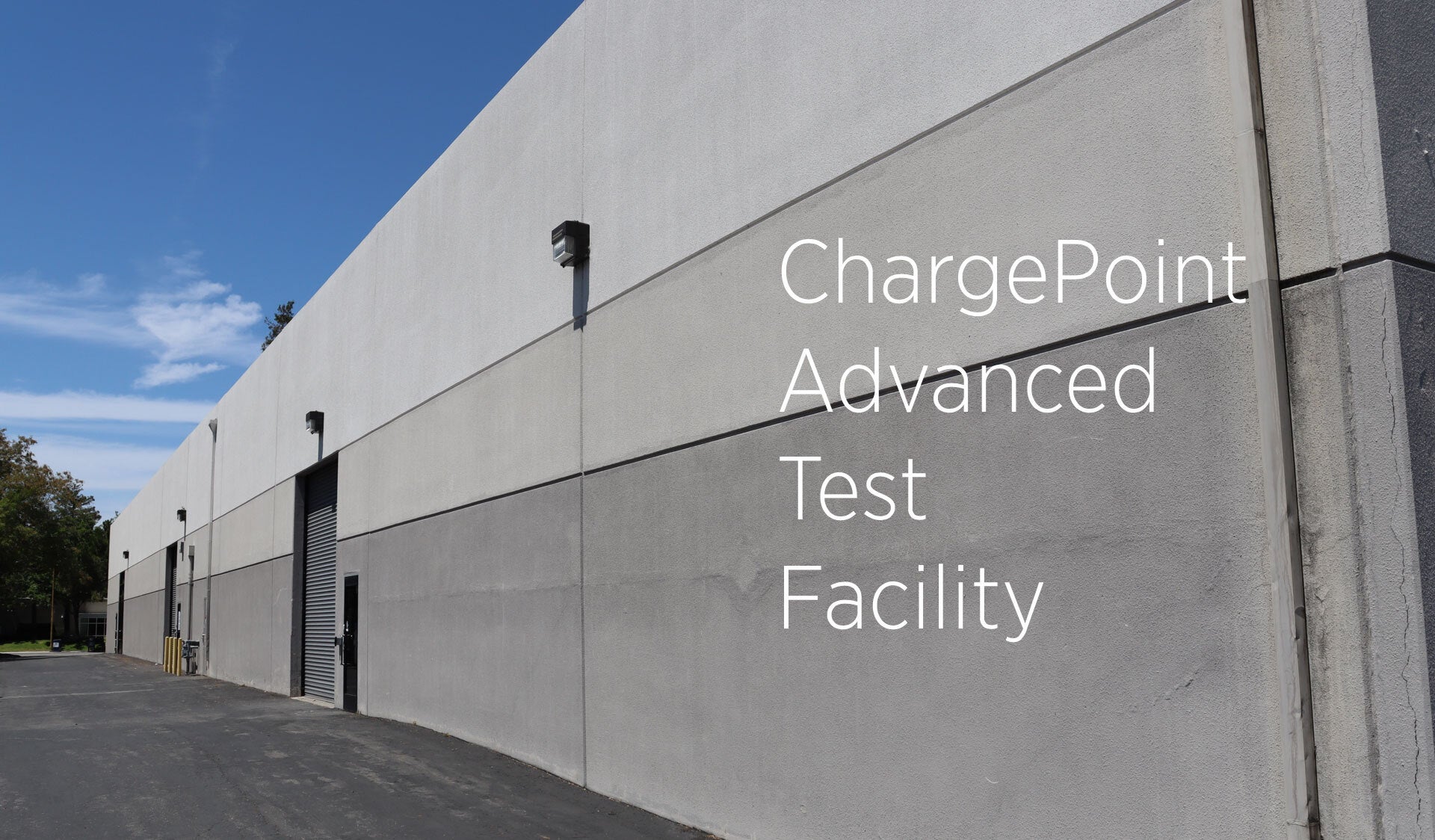
Das Ziel, die weltweite Akzeptanz von Elektrofahrzeugen zu beschleunigen, setzt voraus, dass die dafür nötigen Ladestationen sicher und zuverlässig sind. Deswegen hat ChargePoint erheblich in Qualitäts- und Zuverlässigkeitstests für Hardware investiert. Werfen Sie einen Blick in unsere 1.500 Quadratmeter große, hauseigene Testeinrichtung!
Die innovative ChargePoint Testeinrichtung setzt neue Maßstäbe für die wettbewerbsfähige Produktentwicklung innerhalb der Ladebranche für elektrische Fahrzeuge. Sie umfasst mechanische, Umwelt- und Betriebsbelastungstests, die sowohl an Subsystemen als auch an vollständig montierten Ladestationen durchgeführt werden. Leistungsstarke Testressourcen im Labor - einschließlich mechanischer Prüfvorrichtungen, Mehrfachtestsystem, Thermokammern, Regen- und Sprühtester sowie vielseitiger Hochleistungstests - ermöglichen das kontrollierte Testen statistisch signifikanter Stichprobengrößen. Wir testen während der NPI-Phase (New Product Introduction = Neue Produkteinführung) und der ORT-Phase (Ongoing Reliability Testing = Laufende Zuverlässigkeitstests) bis zum Produktionsende des Produkts (EOL = End of Life), um sicherzustellen, dass unsere Hardware so zuverlässig wie möglich ist und dass dieses Maß an Zuverlässigkeit während des gesamten Produktlebenszyklus beibehalten wird. Diese Tests ermöglichen auch die Bewertung von entwicklungs-, material- und herstellungsbedingten Risiken und die Minderung dieser Risiken mit nachfolgenden Anpassungen im Design.
Mechanische Tests
Unsere Ladestationen wurden für die Belastbarkeit bei Stößen, Vibrationen, Erschütterungen, Stürzen und langfristiger Nutzung sowie dadurch bedingten Verschleiß konzipiert und hergestellt. Bei diesen Tests werden alle kritischen Teile des Systems mechanisch beansprucht, so wie es auch bei der tatsächlichen Nutzung der Fall wäre.
Aufpralltests
Eine Pendeleinrichtung schlägt mit kontrollierter Energie auf die Station auf und simuliert so reale Umstände wie das Werfen eines Steins oder Vandalismus an der Station. Jedes Produkt wird bis zu einer angemessenen Schlagfestigkeit getestet, wobei unsere Schnellladestation CPE250 mit IK10, dem höchsten standardisierten Stoßfestigkeitgrad, getestet wird.
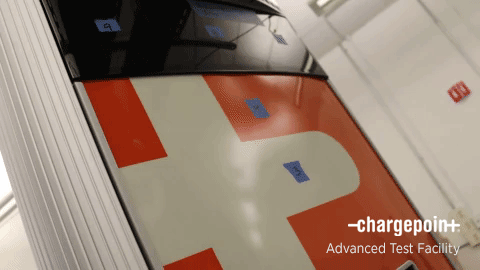
Vibrations- und Falltests
Vibrationen, die von einem hydraulischen Schüttelsystem auf eine Station ausgeübt werden, welche aktiv in Betrieb ist, simulieren die Belastung während seismischer Ereignisse (wie z.B. einem Erdbeben). Hingegen simulieren Vibrationen, die auf eine voll verpackte Station ausgeübt werden, die Belastung während des Transports. Ersteres dient eher dazu, die Sicherheit nach einem seismischen Ereignis zu gewährleisten, während letzteres dazu beiträgt, die Transportrisiken zu bewerten, um eine kontinuierliche Funktionalität aller Stationen bei deren Ankunft zu gewährleisten. Unter der gleichen Prämisse wird auch das voll verpackte Produkt einem Falltest unterzogen.
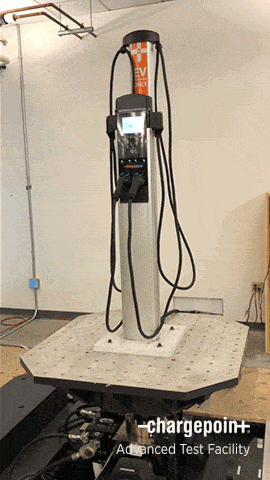
Rotieren des Schwenkarms und Wiederholtes Laden
Um potenzielle Zugkräfte während der Handhabung nachzubilden, wird an den Kabeln jedes Produkts mit kontrollierten Kräften und Richtungen (definiert durch Benutzerstudien) wiederholt gezogen. Um noch einen Schritt weiter zu gehen, führen wir auch statische Last- und Schockiterationen mit hoher Kraft durch, um Szenarien mit aggressiver Handhabung oder Vandalismus durch den Benutzer nachzustellen.
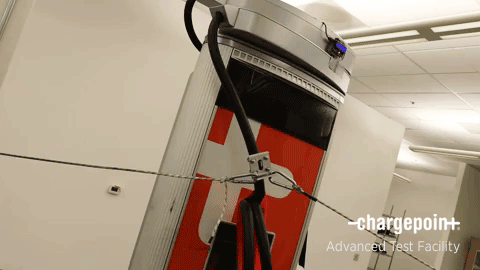
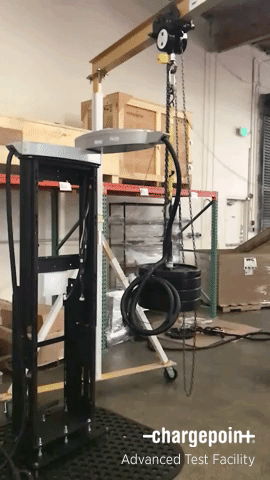
Wiederholtes Aus- und Einstecken des Ladesteckers aus der Halterung
Das Aus- und Einstecken der Ladestationsstecker wird durch speziell entwickelte hauseigene Prüfgeräte automatisiert. Mit diesem Test bewerten wir die Risiken, die mit der Anhäufung von mechanischem Verschleiß verbunden sind (potenzieller störungsbedingter Ausfall von Steckergehäusen, Verriegelungen und/oder elektrischen Kontakten).
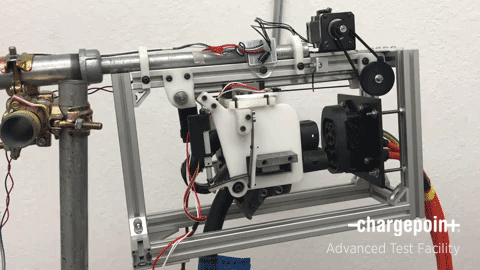
Test unter Umweltbelastung
Bei Umweltbelastungstests werden die Einheiten beziehungsweise die Stationen über längere Zeiträume extremen elementaren Bedingungen ausgesetzt (Regen, Schnee, Wind...), um sicherzustellen, dass sie danach, trotz Einwirkung der Elemente, funktionsfähig bleiben.
Wiederholte thermische und Temperatur- sowie Feuchtigkeitstests
Längere Zeit bei Temperaturen von bis zu 85°C und einer relativen Luftfeuchtigkeit (RH – relative humidity) von bis zu 85% RH belasten elektrische Systemkomponenten und Materialien, die anfällig für Korrosion oder hitze- bzw. feuchtigkeitsbedingten Verschleiß sind. Ein alternatives Testprofil variiert die Temperatur von -40°C bis 85°C (mit unkontrollierter Luftfeuchtigkeit), um interne Komponentenverbindungs- und Integrationsschnittstellen zu belasten, die Unstimmigkeiten des Wärmeausdehnungskoeffizienten (WAK) aufweisen. Dies schließt Teile des Systems ein, die so klein sind wie Lötstellen auf Leiterplatten bis hin zu größeren Klebeflächen und Bolzen, die Rahmen und andere Gehäusekomponenten verbinden.
Von dort erzwingen unterschiedliche Feuchtigkeitsprofile eine wiederholte Kondensation sowohl an den Außen- als auch an den Innenflächen und simulieren damit so etwas wie die Taubildung in feuchten Klimazonen. Dieses Stressprofil wird dann durch veränderte Kammerbedingungen verschärft, die diese Kondensation zum Einfrieren zwingen (da sich Wasser an Systemspalten und auf Komponentenoberflächen zu Eis ausdehnt).
Die oben skizzierten Temperatur- und Feuchtigkeitstests belasten unsere Produkte während und über die vorgesehene Lebensdauer hinaus.
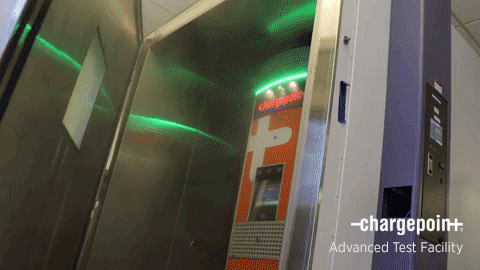
Sprüh-, Staub- und Salznebeltests
Sprühtests helfen bei der Simulation von Regen- und Druckwaschszenarien. Wüstenstaubprüfungen simulieren die Ansammlung von leitfähigen Partikeln über einen längeren Zeitraum. Salznebeltests simulieren beschleunigte Korrosion in Küstenregionen.
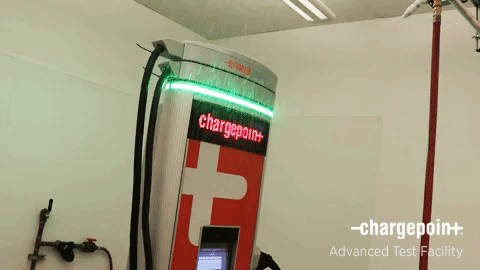
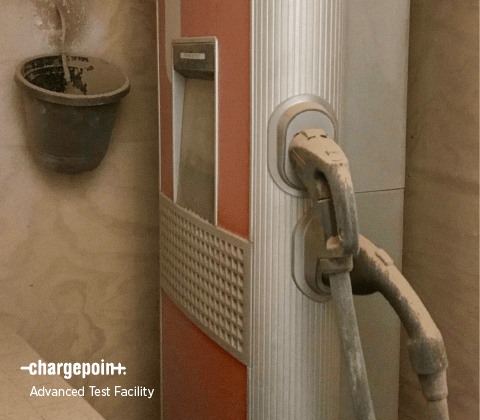
Sonnenbestrahlungs- und UV-Belastungstests
Die Produkte werden dem gesamten Spektrum der Sonnenenergie (Photodegradation) ausgesetzt, wobei die Lichtechtheit, die thermische Belastung und UV-Stabilität geprüft wird. Eine Anordnung mehrerer Hochleistungslampen in einem geschlossenen Bereich gibt die volle Bandbreite des Sonnenspektrums ab, um die Sonnenbelastung zu simulieren, während die Testeinheiten in einer separaten Kammer UVA-Strahlung aussetzt werden.
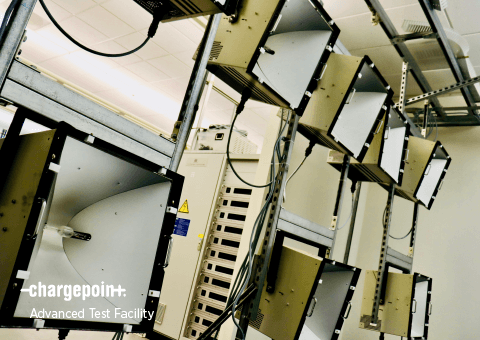
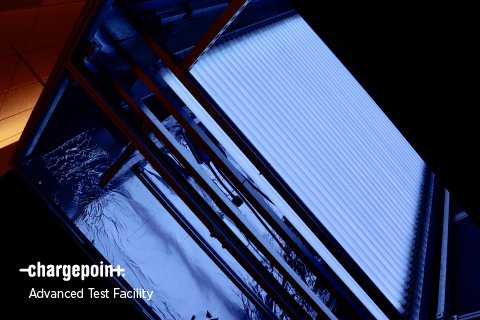
Betriebliche Belastungstests
Die wohl wichtigste Kategorie von Tests, nämlich Langzeit-Betriebsbelastungstests, übt alle kritischen Systemfunktionen unter extremsten Bedingungen aus. Dies erfordert eine python- und/oder BASH-gesteuerte Automatisierung, die den Betrieb des Produkts beschleunigt, um den Feldeinsatz über den vorgesehenen Produktlebenszyklus zu simulieren.
In diesem Test wird die Station in einer erhöhten Umgebung von 50°C getestet, um den Wärmemanagementmechanismus des Systems herauszufordern. Hierbei ist auch ein E-Auto-Simulator integriert, der einen End-to-End-Betrieb durchführt, welcher den Ladezyklus wie bei Fahrzeugen im Feld simuliert. Währenddessen werden die sekundären Funktionen des Systems (wie z.B. Display-Ausgänge, LED-Beleuchtung und sogar die integrierten Lautsprecher) bei maximaler Beanspruchung getestet.
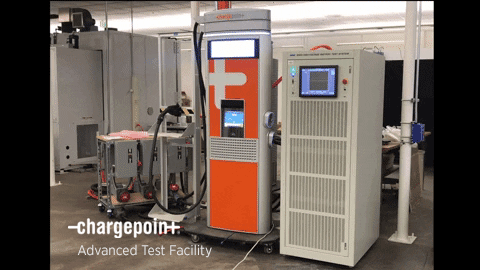
Harte Schläge im Systemtest
Die Tests in der innovativen ChargePoint Testeinrichtung ermöglichen es unseren funktionsübergreifenden Ingenieurteams, Produkte zu entwickeln, die sicher und zuverlässig sind - trotz der intensiven mechanischen, umweltbedingten und betrieblichen Beanspruchung, die sie während ihrer vorgesehenen Lebensdauer im Feld erfahren. Die durch die Tests identifizierten Risiken werden nach Schweregrad, Erkennbarkeit und Wahrscheinlichkeit bewertet, um eine erwartete Auswirkung auf den Benutzer zu bestimmen.
Diese hochmoderne und teure Testeinrichtung macht unser Engagement für die Produktintegrität laut und deutlich. Die Investition in hausinterne Tests bedeutet, dass wir in der Lage sind, sowohl eine breitere Palette von Tests durchzuführen als auch statistische Signifikanz für jeden Test leichter zu erreichen. Für Anbieter, die Tests an Drittlabore auslagern (aus Gründen der Kosteneinsparung), ist dies kaum möglich.
Unsere Testeinrichtung wird immer mit neuer Ausrüstung ausgebaut. Im letzten Jahr haben wir zum Beispiel ein hydraulisches Hochlastvibrationssystem, eine Staub- und eine Salznebelkammer installiert. Die Ressourcen unserer Einrichtung in Verbindung mit unseren immer ehrgeizigeren Produktzielen fördern eine Umgebung für Systemtests, die anderswo schwer zu finden ist.
Möchten Sie unsere innovative Testeinrichtung hautnah erleben? Blicken Sie hinter die Kulissen: